Equipment owners of Woodward face potential risks when they opt for the use of non-Original Equipment Manufacturer (non-OEM) parts or non-authorized service facilities (non-ASF) to remanufacture their valuable equipment. These actions can have dire consequences, resulting in a series of detrimental effects that can significantly impact the owners.
One of the major concerns arising from such decisions is the rejection of warranty and insurance claims. When non-OEM parts are used or repairs are carried out by non-ASFs, the manufacturer’s warranty may be rendered void, leaving equipment owners without any recourse for repair or replacement. Similarly, insurance claims related to equipment failures or accidents may be denied, leading to financial losses and potential legal disputes.
Furthermore, the safety of personnel is also at stake when non-OEM parts or non-ASF repairs are employed. Equipment that does not meet the manufacturer’s specifications or undergo proper testing procedures may be prone to malfunction or failure, posing serious risks to the individuals operating or working in close proximity to the equipment. This can result in personnel safety events, including accidents, injuries, or even fatalities, which could have been preventable by adhering to the recommended OEM parts and authorized service facilities.
In addition to safety concerns, the utilization of non-OEM parts or non-ASF repairs can lead to premature product failure. When equipment is not remanufactured or serviced according to the manufacturer’s guidelines, the lifespan and performance of the product can be significantly compromised. This can result in unexpected breakdowns, malfunctions, or suboptimal operation, leading to costly repairs and operational downtime. The financial burden of frequent repairs or premature replacements can accumulate over time, negatively impacting the overall efficiency and profitability of the equipment owner’s operations.
To mitigate these potential risks and ensure the optimal functioning and longevity of Woodward equipment, it is strongly recommended to utilize Woodward’s regional authorized service facilities (ASFs). By choosing an ASF, customers can avail themselves of the benefits of the factory warranty, compliant with Woodward’s stringent material specifications, testing procedures, and certification agency specifications. This ensures peace of mind for equipment owners, as they are assured of full insurance reimbursements and comprehensive product warranties.
Moreover, relying on Woodward’s ASFs maximizes the life and performance of Woodward valves, actuators, or governors. These authorized service facilities have the expertise, knowledge, and access to genuine OEM parts, allowing them to carry out repairs and remanufacturing processes in accordance with the highest industry standards. By adhering to the recommended OEM parts and authorized repair procedures, equipment owners can optimize the safety, reliability, and efficiency of their Woodward equipment.
Below are visual examples of product failures subsequent of using non-OEM parts or incorrect repair performed by a non-ASF:
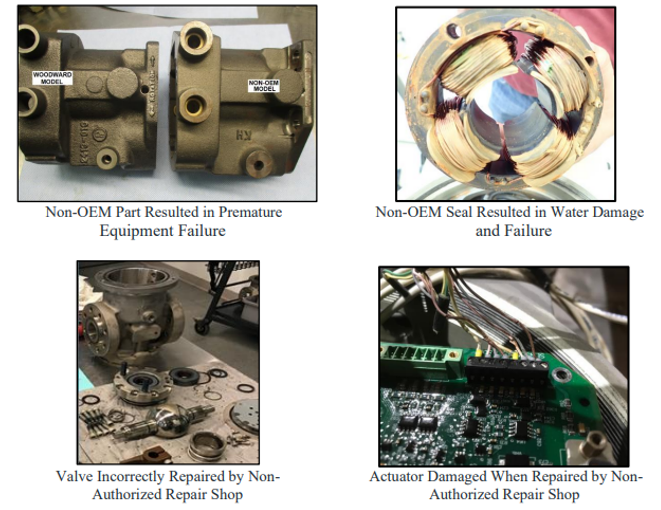